How Does Prefabrication Impact Commercial Construction Costs?
Prefabrication has revolutionized commercial construction projects by reducing costs and time while also ensuring higher quality standards and a safer working environment. Prefabrication refers to the process of constructing building components off-site and then assembling them at the construction site. This can include everything from wall systems and roof panels to piping and electrical systems.
One of the most significant advantages of prefabrication is the cost savings associated with it. According to research, prefabrication can reduce construction costs by up to 20%. This is because it enables the use of standardized components and reduces the need for on-site labor and materials. By manufacturing building components off-site, companies can benefit from economies of scale, which can result in lower costs.
Prefabrication also helps reduce construction time. As building components are manufactured off-site, there is less time spent on-site, resulting in faster construction times. Studies have shown that prefabrication can reduce construction schedules by up to 50%, which can have a significant impact on overall project costs. In addition, off-site manufacturing can take place simultaneously with on-site construction, which can further reduce the overall project duration.
Finally, prefabrication can also improve quality and safety. By manufacturing building components in a controlled environment, companies can ensure that they meet higher quality standards and reduce the risk of defects. In addition, prefabrication reduces the amount of on-site labor required, reducing the risk of accidents and injuries, thereby supporting a safer working environment.
Prefabrication has become an increasingly popular construction method due to the many benefits it offers, including cost savings, reduced construction time, improved quality standards, and safer working conditions. As such, we can expect to see an increasing trend towards prefabrication in commercial construction projects as the construction industry seeks to continuously improve operational efficiency and economic viability.
Common Prefabricated Elements Used in Commercial Construction Projects
One way that prefabrication impacts commercial construction costs is through the use of common prefabricated elements. These elements can help to streamline the construction process by reducing the time and labor required for on-site construction. Here are some of the most common prefabricated elements used in commercial construction projects:
Wall panels: These are pre-made wall sections that can be easily transported and installed on site. They can be made from a variety of materials, including concrete, steel, or wood.
Roof trusses: These are pre-fabricated units that are typically made from wood or steel. They offer several advantages over traditional on-site construction, including increased speed and accuracy.
MEP systems: This stands for Mechanical, Electrical, and Plumbing systems, which can be pre-fabricated off-site and then easily installed on site. This can save significant time and labor costs compared to traditional on-site installation.
Bathroom pods: These are pre-fabricated units that contain all of the necessary components for a bathroom, including plumbing fixtures, shower stalls, and toilets. They can be easily transported and installed on site, reducing the need for on-site construction.
Modular construction units: These are entire building sections that are pre-fabricated off-site and then transported to the construction site for installation. They are often used for multi-unit buildings, such as hotels or apartments.
Staircases: Prefabricated staircases are becoming increasingly popular in commercial construction because of their efficiency and accuracy. They are manufactured off-site, then transported to the construction site and assembled. This process can significantly reduce installation time and costs.
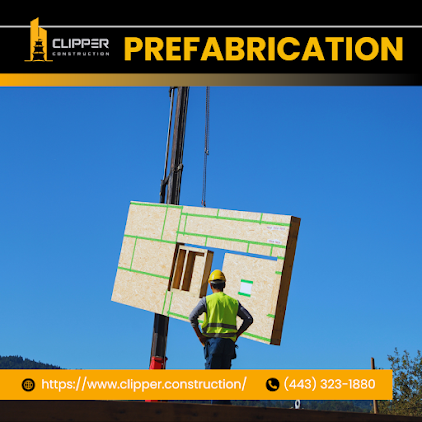
Improving Quality Control with Prefabrication
Prefabrication is an innovative technique that has revolutionized the construction industry. With the use of modular components, prefabrication offers several benefits, including improved quality control. By manufacturing building components off-site, prefabrication provides a highly controlled environment for the production and assembly of building elements, ensuring consistency in quality.
One of the primary reasons for improved quality control with prefabrication is the use of advanced technology in the manufacturing process. The use of computer-aided design (CAD) and computer-controlled machines allows for a high level of precision in the production of building components. The process is completed with a high level of accuracy, and every component is checked before leaving the factory.
Prefabrication also enhances quality control by reducing on-site construction time. Building components manufactured off-site can be easily transported to the construction site and assembled quickly. This not only increases efficiency but also allows for more supervision during the installation process. Further, prefabrication helps to eliminate on-site errors, inaccuracies and deficiencies that may shorten the lifespan of buildings.
The potential to improve quality control is one of the many benefits of prefabrication. The technique has transformed the construction process by allowing for quality management to become more rigorous and precise. By enhancing efficiency, accuracy, and control, prefabrication has the potential to create more sustainable, durable, and cost-effective commercial buildings for years to come.
Innovative Applications of Prefabrication in Commercial Construction
As technology evolves, so does the scope and potential of prefabrication. Below are some innovative applications of prefabrication in commercial construction.
1. Prefabricated Building Envelope Systems
Prefabricated building envelope systems can be used in a variety of commercial construction projects, including office buildings, hotels, and retail spaces. The systems consist of pre-manufactured modules that contain structural components, insulation, and outer cladding. By manufacturing these modules offsite, builders can reduce construction times and improve quality control. Additionally, prefabricated building envelope systems can help reduce carbon emissions in the construction industry, making them ideal for eco-friendly construction projects.
2. 3D-Printed Construction Elements
3D printing technology is revolutionizing the way construction materials are manufactured. Builders are now able to print building elements, such as walls and columns, using 3D printing technology. This technology can substantially reduce construction times and costs when compared to traditional construction techniques. Additionally, 3D printing enables builders to print unique and intricate designs that were not possible with traditional construction methods.
3. Modular Construction
Modular construction is a prefabrication technique where entire sections of a building are manufactured offsite and assembled on the project site. This process provides greater flexibility and faster results than traditional construction methods. Modular construction can be used in a wide range of commercial construction projects, including hotels, office buildings, and healthcare facilities. This technique also reduces waste and enhances efficiency, as factories manufacturing modules have the ability to reuse and recycle materials.
Challenges of Prefabrication as Compared to Traditional Construction Methods
One of the significant challenges of prefabrication is the high initial investment cost. The fabrication of materials, transportation, and installation requires specialized equipment, labor, and facilities that add to the overall cost of the project. Moreover, the design and planning phase of prefabricated structures require additional fees for software, pre-construction planning, and quality control inspections. However, despite this cost, prefabrication might help save costs in the long run by reducing material waste and increasing construction efficiency.
Another challenge of prefabrication is the need for stringent quality control measures. The manufacturing phase of prefabricated components requires an exceptionally high degree of accuracy and precision that traditional construction does not require. Even the smallest deviations from design and dimension can significantly affect the assembly process, causing errors, and, ultimately, delays. As a result, every component must be carefully inspected before installation to ensure that it meets the required specifications. This makes prefabrication more time-intensive but ensures that the final product is of higher quality and more efficient than traditional construction methods.
Finally, the transportation and logistics of prefabricated components can also present a challenge. Prefabricated components are typically much larger and heavier than traditional building materials, requiring specialized transportation and storage. The logistics of transporting and storing these components must be carefully planned to minimize the risk of damage, delay, and costly mistakes. Also, constructing using prefabrication requires specialized equipment and labor that might not be available locally, which may incur additional transportation costs or even import fees.
Prefabrication presents numerous advantages over traditional construction methods, such as reduced costs, faster construction times, and increased safety. However, it also poses its own set of challenges. Ensuring the initial investment cost, maintaining a high degree of quality control, and managing transportation and logistics are just some of the obstacles prefab construction presents.
Conclusion
In conclusion, prefabrication techniques have shown significant cost savings and time reduction in commercial construction projects. This method has proven to be efficient in reducing material waste and labor costs while ensuring high-quality products. It allows contractors to streamline the workflow and reduce on-site construction time, resulting in a faster return on investment. Additionally, prefabrication allows for greater customization and provides easier maintenance and repair of buildings. Overall, implementing prefabrication techniques in commercial construction can have a positive impact on the overall costs and timelines of a project.
Contact Details:
Full Address: 1354 Cooksie St, Baltimore, MD 21230
Phone Number: (443) 323-1880
Website: https://www.clipper.construction/
Business Hours: Monday to Friday, 6:00 AM to 7:00 PM
Google Maps: https://goo.gl/maps/bf9Lsd2GPQrMfZfW6
Google Site: https://sites.google.com/view/clipperconstruction
About Us:
Clipper Construction is a tech-enabled Commercial General Contracting firm providing construction services across several verticals including retail/office fit-out, adaptive reuse, historical restoration and mixed-use development.
Clipper Construction leverages technology to drive efficiencies in the construction process to ensure projects are on schedule, on budget and exceed our clients expectations. We are also leveraging our background in technology to create a better client experience with our custom client platform we designed to provide more transparency and better communication than our competition in this space.
Social Links:
YouTube: https://youtube.com/@clipperconstruction
Facebook: https://www.facebook.com/clipperconstruction/
Twitter: https://twitter.com/buildclipper
Instagram: https://www.instagram.com/clipperconstruction/
Blogger: https://clipperconstruction.blogspot.com/
WordPress: https://clipperconstruction.wordpress.com/
LinkedIn: https://www.linkedin.com/company/clipper-construction/
Pinterest: https://www.pinterest.ph/clipperconstructioncompany/
Business Site: https://business.google.com/website/clipperconstruction/
Frequently Asked Questions:
What are the Typical Stages of a Commercial Building Construction Project
What are Some Things to Consider Before Choosing a Commercial Construction Company?
What are Some Advancements in the Commercial Construction Industry?
How Do You Ensure That Commercial Construction Projects Are Completed Within Budget and on Schedule?
Is Design-Build the Best Approach For Commercial Construction?
What Commercial Construction Stages Do Project Managers Oversee?
How Can I Find A Reliable and Reputable Commercial General Contracting Service In My Area?
What are the Benefits of the Design-Build Construction Process?
What is the Difference Between Pre-Construction and Construction Project Management?
How Does Prefabrication Impact Commercial Construction Costs?
What Emerging Commercial Construction Technologies Are Improving Green Building Practices?
What are the Primary Factors to Keep in Mind When Planning a Commercial Building Renovation?
How Can Technology Be Used to Improve Productivity in Commercial Construction?
What are Ways of Managing Risks During the Construction Process?
What are the Advantages of Using CAD in the Building Design and the Construction Industry?