AssalamuAlaikum & Greetings Everyone!
AssalamuAlaikum & Greetings Everyone!
I am glad to see that the 2nd week has ended and we are in 3rd week of the season 21, thanks teacher @yolvijrm for this wonderful lecture on Costing methods.
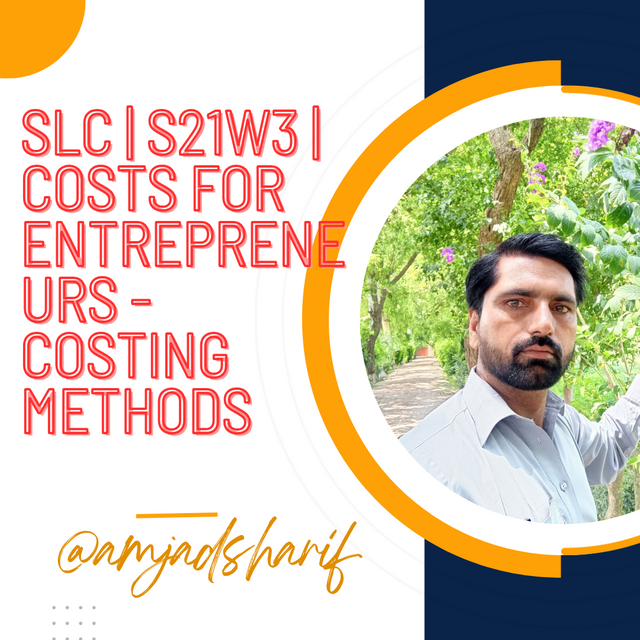
Q.1 - What are costing methods and what is their importance?
Costing Methods and Their Importance |
---|
Costing methods are simply procedures that help various businesses to establish the cost of various products, services or goods to be offered. Such methods assist in tracking of expenses, determination of prices and therefore promoting the achievement of profits by various companies. It is a critical factor to consider when doing business in today’s world, more so when operating in a cut throat market. Here are some of the most used costing methods and why are they useful?
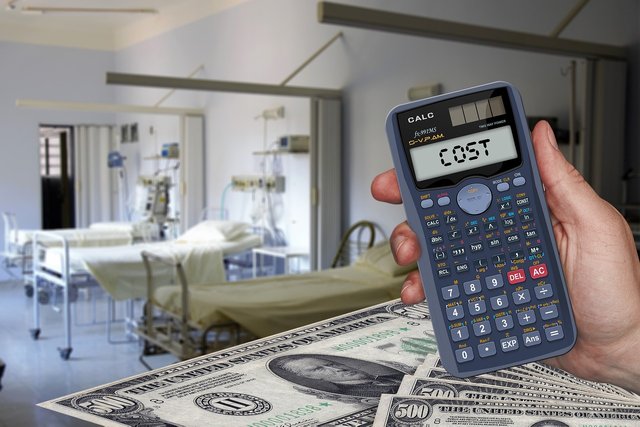
source
1. Job Costing
Job costing is used in a manufacturing environment where products are made according to customer order. Each job is indeed different and as such; costs associated with it are also separately recorded. This method is most suitable for organisations such as construction companies, custom furniture manufacturers or a printing firm, where every contract may differ in terms of inputs, materials, labour and time.
Importance: Job costing is especially helpful because it ensures companies know the cost of products and services offered by the business which helps set some of the best prices which can enable the business know the level of profitability of individual projects that have been tendered.
2. Process Costing
Process costing is applied where products are standardized and produced through a production line similar to food manufacture, chemical production or textile industries. In this method, all costs are spread over all units of production in a particular period of time.
Importance: Cost-volume-profit analysis helps companies to adopt techniques of exercising control over costs when producing products in a large number, by giving the companies an idea of the average cost per unit that is incurred in the process, so as to be in a position to actually fix the price of the products and by so doing be in a position to know whether or not the business is profitable enough.
3. It is also referred to as Activity Cost Analysis (ACA):
This approach of costing accords costs to products and services flowing from the activities involved in their production. In this method, different activities that are involved in production process are recognized and costs are allocated appropriately. It is usually employed in enterprises that have high fixed costs, such as manufacturing or providing of service.
Importance: ABC makes a business aware of indirect costs that are associated with a particular product so that correct pricing strategy can be taken in an effort to manage costs.
4. Standard Costing
Standard costing entails the setting up of standards costs for products or services and then comparing the standards costs. This method is widely applied in manufacturing sectors in the process of providing budgets and evaluating performances.
Importance: It assists business in cost control since it compares standard cost and actual cost. This way, companies can correct actions that have led to such inefficiency, or prevent them in the future.
5. Marginal Costing
The marginal costing or variable costing highlights the cost of manufacturing one additional unit of product. This method only takes into account the variable costs, that is costs which vary directly with the level of production and leaves out the fixed costs.
Importance: Users find marginal costing useful: for deciding the minimum selling price; for fixating production levels; and for assessing the profitability of further production.
The Significance of Costing Methods |
---|
Accurate Pricing: Pricing strategies assist organizations to find the correct price for their goods and services. Knowing all types of cost makes it possible for the firms to fix their prices to reflect the cost of production and earn profit.
Profitability Analysis: Costing methods also give information on areas that are generating incomes and what areas we should avoid since they are not generating any considerable incomes. This not only enables a firm to exploit more profitable products at the expense of the less profitable ones but also enhance the efficiency of the less efficient activities.
Budgeting and Forecasting: Understanding the cost structure of products is important in planning other costs as well as performing general forecasting. This is more effective in a way of controlling of the finances and it assists in establishing more achievable financial objectives.
Cost Control: When costs are dissected from one or the other angle, it becomes inexpensive to determine potential areas of over expenditure in theorganization. This results in enhanced costs control and hence higher profitability.
Decision-Making: The costing methods are an essential aspect of attaining essential information for the business decisions to be made. If a business is choosing between different projects, or choosing whether to stop producing a particular item, or scale up, for example, then it is important that the business has the right cost data.
Concisely, costing methods are another essential weapon in company’s arsenal, helping to control cost, determine reasonable price level and secure utmost profit. The right costing method assists the company to deal with financial risk, adapt to its problems, reduce cost and make proper strategic decisions.
Q.2 - Explain the difference between the job order and process costing methods.
Job Order Costing Vs Process Costing |
---|
1. Job Order Costing:
What it is: This method is used when products are produced to customer orders. All jobs or orders are different, similar with furniture or clothes made to order or particular constructions.
How it works: Expenditures are also recorded based on the type of job that is being done. These include the cost of materials used in a particular job, cost of man power in each job, cost of factory overheads recovered for a particular job and all costs are accrued into a job number. Finally at the end of the job the total cost is worked out.
Where it’s used: For the most part in industries, which work on specific order requirements for their products, such as construction firms, printers, or specific production based companies.
2. Process Costing:
What it is: This method is applied when similar products are produced in batches, for example in food processing, factories, chemically based industries or cement industries.
How it works: The costs are recorded for every step known as a process of producing a thing. Co-variation or apportionment is a costing approach that averages costs throughout total units manufactured in that process rather than charging costs to specific orders. This way, the cost per unit is ascertained Due to this, the cost per unit is arrived at.
Where it’s used: Pervasive in organisations that generate many standard output, such as oil refineries, beverage makers, and textile producers.
Feature | Job Order Costing | Process Order Costing |
---|---|---|
Product Type | Customized or unique products | Mass production of similar products |
Cost Tracking | Costs tracked by individual job | Costs tracked by production process |
Industries | Construction, Printing, Tailoring | Food Processing, Chemicals, Cement |
Cost Calculation | Cost per job | Cost per unit (averaged) |
Q.3 - Research and explain, to the best of your understanding, two costing methods different from those explained in this class.
Let's explore two other distinct costing methods: The two main approaches of cost control are Marginal Costing and Standard Costing. The above methods are not common conventional approaches and each of them has its strengths and weaknesses.
1. Marginal Costing
Marginal costing also referred to as variable costing, emphasizes additional cost that is attributable to the production of one unit of a product. IFOA assumes only variable costs for inventorable costs like material costs, direct labour costs, while fixed costs such as rent, salaries are considered as period costs. It is more useful in the short run since it does not allow for looking out for the company’s best interest in the future.
How It Works:
Marginal cost occupies a special place as it is estimated on the basis of change in total cost that takes place where the quantity produced is altered by one unit. For instance, if a cost of making an extra unit of production is $50 of materials plus $50 of labor, then the marginal unit cost is $50. It this method enables businesses to determine their pricing strategies, their production capacity and whether to accede to special orders.
Advantages:
- Simple to Understand: It is easier to compute since only variable costs will be included; therefore, it is quite easy for the management to compute.
- Better Short-Term Decisions: assists in making quick decisions on pricing, production decisions and whether to take on more orders at the company.
- Focuses on Contribution Margin: By using the contribution margin inclusive of the sales price and variable cost, one is able to identify product profitability.
Disadvantages:
- Ignores Fixed Costs: For it does not assign any fixed costs to products, it can provide a skewed picture of the marginal cost of producing goods.
- Not Suitable for Long-Term Pricing: Adopting marginal costing as the base for making the price can be dangerous where fixed costs are high.
- Limited Use: It is not ideal for use by firms who have many cost which are fixed for a given time or where exact product costing is paramount.
2. Standard Costing
Standard costing therefore is a way of pre-setting the costs of products with the help of historical costs, industry costs or even future costs. These so called “standard costs” are used as a reference against which actual cost are measured. Cost control and improvement are conducted through comparing deviations between standard and actual costs.
How It Works:
Firms estimate standard costs for each material, the labor, and manufacturing overhead used in the production process beforehand. For these, they always want to analyze and compare the standard costs to the actual company costs after production. The difference is referred to as a ‘variance’ whereby through comparison an organization is able to unravel factors that led to even bigger cost savings or potential flaws.
Advantages:
- Cost Control: It assists to evaluate the costs which are exceeding or below the standards through detecting such variances, so that corrective steps could be enforced by the management.
- Budgeting and Forecasting: Convenient in the preparation of a financial forecast and help in the preparation of the expected cost of production.
- Performance Evaluation: It can be also used to compare the performance of one department or cost center against another.
Disadvantages:
- Time-Consuming Setup: Most of the time standard costs involving so much data and details to estimate takes quite a lot of time to determine.
- May Not Reflect Reality: Standard costs may prove to be a cause for a problem if they are not reviewed from time to time and hence lead in giving wrong cost assessments.
- Focus on Cost Reduction: While stressing cost variances, some managers may start looking at ways of minimizing costs, which in the longer run could mean a lower quality product or fewer new products.
To be definite, each of the two techniques— Marginal Costing and Standard Costing—is useful in its own way. Use of Marginal Costing is most appropriate in short-term decisions and special pricing situations, whereas the use of Standard Costing should be more appropriate in the overall control of costs, planning and control of budgets, and performance evaluations. However, each of the above methods has its weaknesses that businesses must address depending on the kind of business and industry they are in.
Q.4 - Perform the costing by work orders, according to what was explained for a cake manufacturing business,
In order to do a costing by work orders for a cake manufacturing business the following steps should be followed. The objective is to identify fixed and variable manufacturing costs that should be applied against certain work orders in order to ascertain the overall cost of each cake. Here's a step-by-step guide:
Step 1: Understanding the Work Order
A work order is a specific document that will contain the precise instructions to create a set of cakes. It includes information like:
- Flavor of cake (chocolate, vanilla, red velvet and etc.)
- Quantity (number of cakes)
- Special request (ornamental and beautification request, menu restrictions)
- Delivery date and time
Step 2: Breakdown of Costs
The total cost of producing cakes as per a work order can be divided into four main categories:
- Direct Material Cost
- Direct Labor Cost
- Manufacturing Overhead
- Except for direct and administrative costs all other expenses are kept miscellaneous.
Step 3: Costing of Direct Material
This means the amount of money that you are going to part with to get all the ingredients needed for the cake preparation. Here's how to calculate it:
- Write all Directions, procedures, and all other uses of Ingredients (e.g., flour: is used for thickening or coating, and baking the dough; sugar: used for sweetening),
- Calculate the Proportions Required per Cake (according to the regular serving sizes for baking)
- Estimate the Cost per Ingredient based on today’s prices to know the amount you need to spend in order to make it to the list.
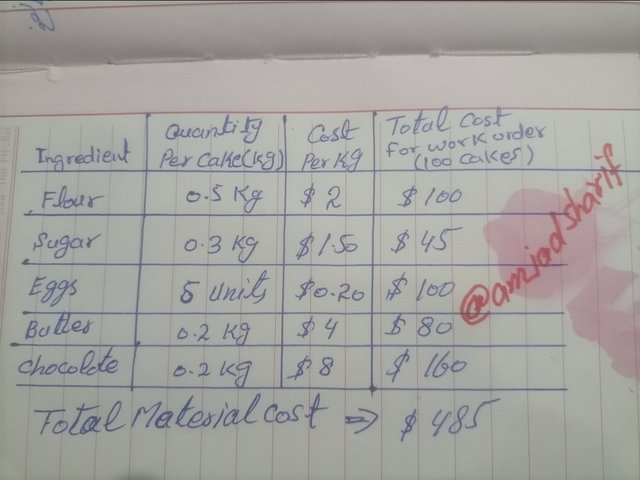
Step 4: Calculating Direct Labor Cost
Labour cost is considered the expenses accrued towards paying the employees bran who is involved in baking, decorating the cakes and packaging.
- Recognise those employees who are to be involved in production specialisations (bakers, decorators, packers).
- Predict the Time needed per cake or per batch.
- Determine the Hourly Wage per each staff person.
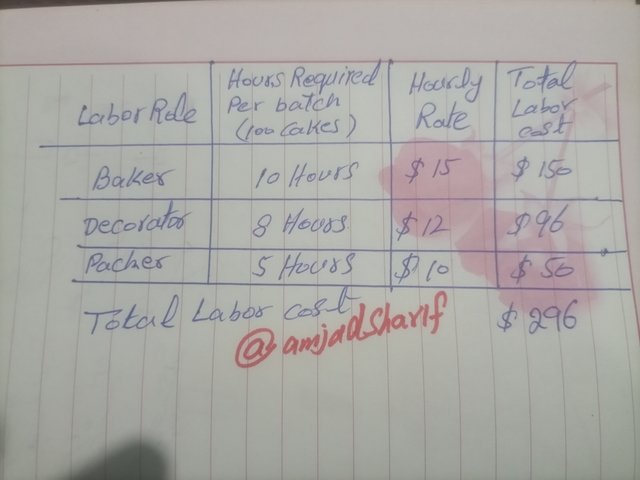
Step 5: Preliminary computation of Manufacturing Overhead
These are production costs which are not directly attributable to the manufacture of the goods including cost of utilities, equipment maintenance cost and cost of kitchen where the product is produced.
- Approximate Monthly Overhead Expenses (like power, fuel, lease, and other consumables on equipment wear and tear etc).
- Disburse Overhead Costs according to work order and the amount of production expected.
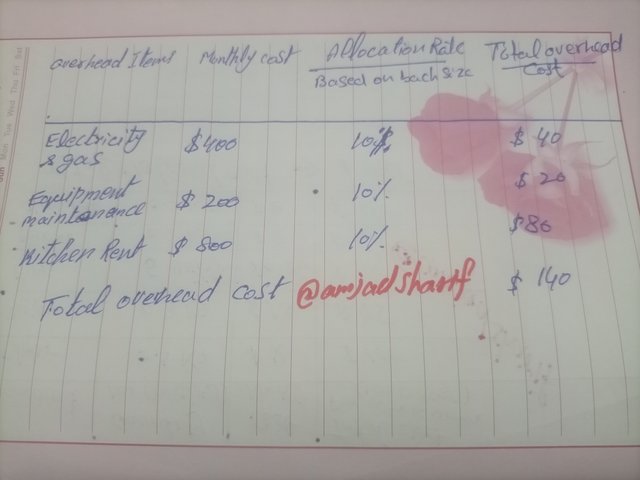
Step 6: Calculating Administrative & Miscellaneous Costs
These costs are for packaging related expense like materials, delivery,
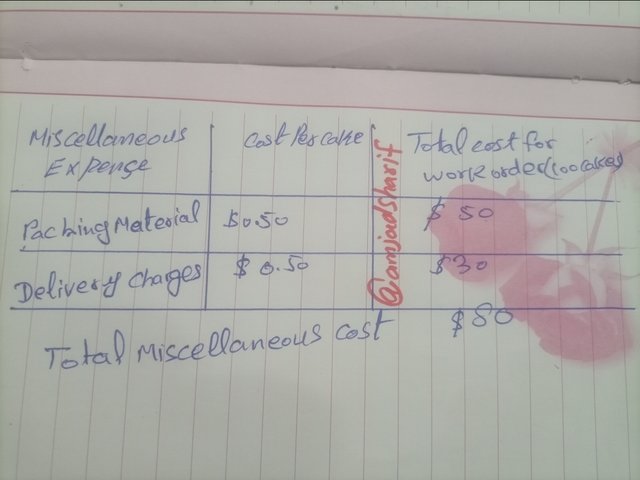
Step 7: Summarizing the Total Cost for the Work Order
Now, add up all the costs calculated in the previous steps to get the total cost of the work order.
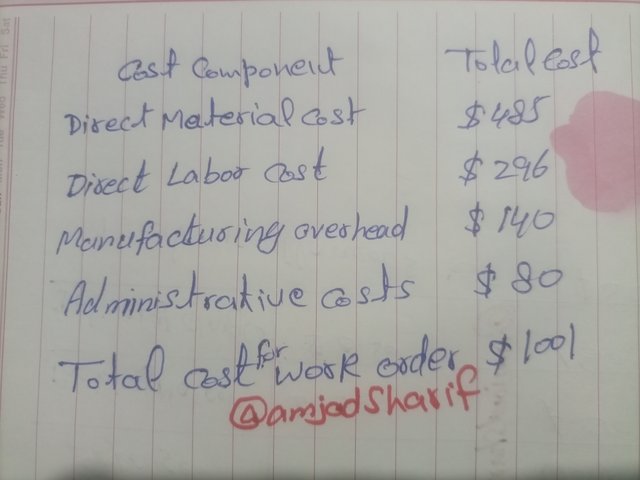
Step 8: Determination of Cost per Cake and Determination of the Selling Price
- Cost per Cake = Total Cost/ No of Cakes
- Dividing the total earnings by 100 and then by the number of cakes produced gives us $1.0010 per cake.
- Selling Price Mats (with a gross profit margin of 30%)
- Selling Price per Cake = Cost per Cake + Cost per Cake × Profit Margin
- Cost of cocoa powder = $ 10.01 Along to this cost, cost of other ingredients also increases by 1.3, cost per cake = $ 13.01
When it comes to this specific work order – 100 cakes, it costs $1,001.00 to produce making $10.01 per cake. In order to meet a targeted profit margin of 30%, the price of selling the cake should be as $13.01.
By the help of this costing method, it is easy to canvass for the prices in conformity to the work orders other than the general market requirements and still make profits.
I am inviting @eliany, @saintkelvin17, and @shabbir86 to participate in it.
Thank You
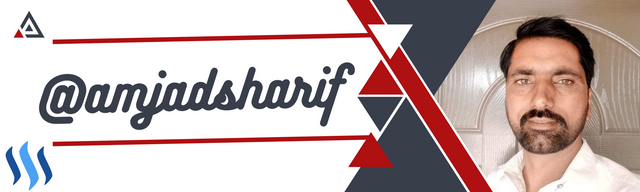
https://x.com/AmjadSharifWat1/status/1856584597896663383?t=vtywvsakfzRm5_vBAW8CAQ&s=19
Downvoting a post can decrease pending rewards and make it less visible. Common reasons:
Submit
Financial management skills are an entrepreneur's most important tool.
Finally good luck for the contest.
Downvoting a post can decrease pending rewards and make it less visible. Common reasons:
Submit