The research team at Northwestern University has created a minuscule walking robot that measures only 0.5 mm in width and is capable of bending, twisting, crawling, walking, turning, and even jumping.
The realm of robotics is a thrilling area of study, and the creation of microscale robots is an engaging area for academic investigation. One can envision these minuscule robots as capable of repairing or constructing small structures or machines within the industry, or serving as surgical assistants to remove blockages in arteries, stop internal bleeding, or eradicate cancerous tumors, all through minimally invasive procedures. Despite the difficulty in achieving controlled movements at such small scales for terrestrial robots, this technology enables various motion modes and can walk at an average speed of half its body length per second.
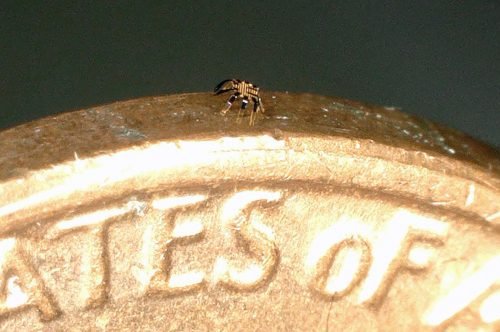
The research team's small robot doesn't require complex hardware, hydraulics, or electricity for its operation. Instead, the robot derives its power from the elasticity of its body. The team constructed the robot using a shape-memory alloy material that returns to its original shape when heated. They used a laser beam to quickly heat specific areas of the robot's body, with a thin layer of glass restoring each location to its original shape upon cooling. The robot's movement arises as it shifts from one phase to another - deformed to remembered shape and back. The laser not only activates the robot remotely, but its scanning direction also dictates the robot's walking direction. For instance, a left-to-right scan causes the robot to move from right to left. The small size of these robots allows them to cool rapidly, enabling them to move at a faster pace as their size diminishes.
The researchers employed a manufacturing method they had previously introduced called the "pop-up assembly method," which takes inspiration from a children's pop-up book. To create the small robot, they began by making precursors to the crab-like walking structures in flat, planar geometries. These precursors were then attached to a rubber substrate that was slightly stretched. When the substrate is allowed to relax, the crab structure experiences a controlled buckling process, causing it to "pop up" into specific 3D shapes. This technique allowed the researchers to produce robots of different sizes and shapes.
Reference articles: