In my first post I would like to share with you this project of the Machine Design course from Simon Bolivar University in Caracas, Venzuela. This project consisted on designing a tool that can be installed on a drone.
In this case, my colleagues and I designed a tool for a branch cutter drone.
The reason why we decided to design a cutter drone is due to the fact that in many occasions it is necessary to remove the branches of the trees either for aesthetics or because the presence of this branch puts the community at risk. An example of this would be the transit routes, since due to regulations and established laws, these should be totally cleared.
We consider that a worker drone would be ideal for the accomplishment of this task because, in the majority of the cases, the accomplishment of this is risky for being a work of height. In addition, generally not only the workers who will perform the work are needed, but at least one crane and a mechanical saw must also be available. In the case of using a drone to carry out this work, a great part of the risks that this work carries with it would be avoided.
Design Procedure (Alternatives)
In principle, it was considered to use a pair of drones, one that would hold the branch and another that made the cut However, this presented a disadvantage in the sense that there was a probability that the drone that made the cut would be lifted at the time of making the cut due to the normal component that is generated in the blade, so it could not be guaranteed that the drone made a continuous cut. Nevertheless, this option had the advantage that there would be a lower load in each of the drones, since there would be a better distribution of the tools.
The second option that was considered consisted in having the same drone subject to the branch and at the same time carries out the cut. This option has the advantage that the link with the branch guarantees to a greater extent the ability to make the cut, another advantage is that it is very similar to the way we perform the cutting of a piece. In fact, when we make a rudimentary cut with a saw, we usually use one of our arms to hold the piece and with the other we make the cut, this is intuitive but it is due to what was explained above. However, it has the disadvantage that the drone would have to support more weight because both tools would be concentrated in a single drone. It was decided to choose to use only one drone, because we consider that the ability to perform a good cut has priority over weight limitation.
Procedure to Perform Cutting:
- The drone is raised to a height that matches the branch to be cut.
- The drone is moved horizontally towards the branch until it stops between the positioner and the branch. Height differences should be corrected by the positioner.
- The arm of the clamp is activated to hold the drone to the branch.
- The arm of the blade is activated to perform the cut (downward movement).
- The cutting arm is removed (upward movement).
- The clamp of the branch is removed.
- The drone is removed from the cutting area.
Final Design Proposal
The way we decided to operate the arms is the same in both and consists of a system of one degree of freedom in which we have a nut that pivots with respect to the arm and acts as a slide with respect to the screw, so that when operating the power screw with the motors, which in turn are placed in pivoting bases, causes a rotational movement in both the arm and the base system.
In the case of the blade, it will be driven with a system of pulleys whose motor is placed on the same cutting arm. It was decided to place a positioner in order to facilitate the fastening of the drone to the branch, so that it had a range of acceptable heights at which the drone could approach the branch and the positioner would finish placing the drone in position correct. Another thing that is worth mentioning is that the same grip plate to the drone is extended so that the battery is placed as a counterweight to the tool, taking advantage of the need to place a counterweight with the need to place a battery. Below is an image of the device, made with Solid Works.
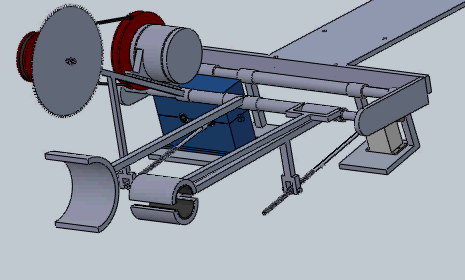
Calculations
To begin with the design procedure, it was first necessary to determine the tangential and normal reactions produced on the disc at the time of cutting. It is worth mentioning that this study was carried out for the wild pine species, which is the most studied species in terms of the circular saw.
Because a motor is desired as light as possible, it was decided that the cut was performed very gradually, for this case is recommended V = 1.5 mm / s. With the suggested value, 0.49 hp is required to operate the blade.
Kinematics of the Arms
On the other hand, using a kinematic study (1 degree of freedom) was determined the speed of the slide (nut) from which the RPM of the power screw can be obtained with the following formula:
w_screw = V_nuer * l
Where l is the pitch of the screw, giving a speed of 20 RPM.
Forces on Power Screws and Gears
The torque required to drive the blade arm power screw was 0.136 Nm. A nominal diameter for the 6mm screw was chosen with a pitch of 1mm. The coefficient of friction used for friction between steel and steel was 0.74 (static worse condition).
With the torque and speed of operation, the required power was obtained, which was about 0.274 W. A 5 rpm motor was chosen and a speed amplification transmission was designed with steel gears whose resulting module was m = 1.25mm. Finally, the diameter of the large pinion is 100 mm and that of the small 25 mm.
In the case of the power bolt of the clamp, this is much less demanded axially (it is guaranteed to be self-locking and resisting), however, it must handle more RPM because the mechanism must be able to attach to the branch to a considerably faster speed. In our case we chose 22.35 degrees / s for which 80 RPM is required in the screw and a power of 0.854 W, so an 80 RPM motor was chosen.
Selected Components:
Couplings: SKF Flex. This coupling was chosen because it is capable of absorbing vibrations and withstanding high shock loads and also solve misalignments. It was decided to have these characteristics due to the vibrations that are transmitted by the fluctuations that occur when making the cut.
Belt and Pulleys: Browning Manufacturing Company Method. It is concluded that it is a Type A belt, with a driving power of D = 4.8 inches, width of ¾ inches and a channel, and a driven pulley of d = 3.2 inches, width of ¾ inches and one channel. This belt is estimated at 43314 hours of service. It should be mentioned that the motor of the blade is placed on a slide that allows to readjust the distance between the pulleys and maintain the tension in the belt.
Charge capacity required:
Time required to perform the task is: 2 min (hold) + 1 min (cut) + 1 min (landing).
With all the components that have been chosen, the estimate of the weight comes from de next consideration: 43.07% Steel (Motor Included). 55.47% Aluminum. 1.46% Plastic. That gives us a total of 13.8 kg. + 2.6 kg (battery).
Drone selection
Now we need to chose a drone that satisfy all our requirements. The Freefly Systems ALTA UAV has a 18 kg capacity and a 10 min of autonomy with a full battery load. That means this drone is perfect for our machine.
I hope that you like our work, and I would love to read any comments that you have about it.
✅ @gjimenezg, I gave you an upvote on your first post! Please give me a follow and I will give you a follow in return!
Please also take a moment to read this post regarding bad behavior on Steemit.
Downvoting a post can decrease pending rewards and make it less visible. Common reasons:
Submit