Comminution- The art of Reduction (Part 1)
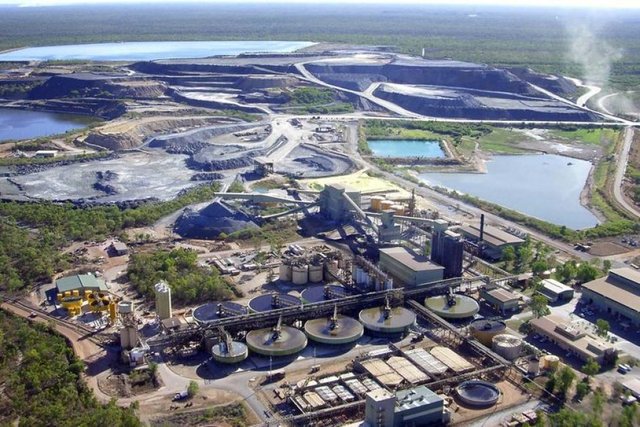
An aerial view of a mining site
Language, religion, fashion, culture, food, transport, people, animals. What do all these factors have in common? Diversity. Every individual country on Earth has their own set of factors that are unique to that specific country. We do however share a few similar interests and one of these interests , which contributes to a large portion of our respective countries economy, is mining. Mining is a process that occurs manually whereby the natural gems and valuables produced by the planet is extracted from beneath the surface and processed to become useful objects in our everyday lives, but have we ever wondered about the process that takes place to provide us with these objects of beauty and lust. In this post, I will be elaborating on the one of those processes, referred to as Comminution.
Comminution is the process applied on many, if not all, mining sites upon the extracted material. During the mining process, certain procedures are done underground, such as explosions, to remove the valuable material from the ground. When these minerals are removed, they often do not come out pure, as in, the compound removed does not only contain that specific material, but also impurities such as sand, rock, organic tissue of deceased organisms and so on. Comminution is the process of transforming this large mixtured lump into its smaller valuable components and discarding of the impurities. Comminution works on the following principle:
If energy is added to a large extracted particle, the outcome of this process will be the production of a smaller particle but also with the addition of sound as well as heat, to apply to the Law of Conservation of Energy. Comminution occurs in many steps and therefore is broken down into the following procedures, that will all be explained during this post:
Size Reduction
Size reduction in the mining industry is the main focus of Comminution whereby the impurities are removed from the extracted product and we then scale this large mass down to more appropriate sizes for manufacturing purposes. The list underneath this heading are processes that allow size reduction to be possible. Although size reduction is the objective rather than a process, we include it in our steps because we need to understand what type of material/mineral we are working with and we need to identify certain parameters. These parameters will assist us in the choice of the processes that will follow, hence, this is the reason we include size reduction in our steps.
For Comminution to be achieved, we must not undergrind or overgrind and we will need to select the optimal equipment to be used for the correct size reduction to occur. In order to do so, we will need to identify the type of feed material to be used. In order to identify the feed material, we use certain parameters, as these parameters help us to identify the energy requirement of the material to be broken down and therefore the status of certain machinery to match those energy requirements.
The parameters to be used are the Standard Bond Grindability Test (which is used to evaluate the crushability and grindability of the feed, which is often referred to as the Work Index) which then can be used the calculation of the Specific Grinding Energy (also a parameter) as well as the Abrasive Index (which is already recorded for all material types) which gives us an indication of the influence on the wear rate.
The Standard Bond Grindability Test/Work Index:

W.itest – Bond Work Index (kWh/t)
P.1 – classifying screen size (microns) - each material has its own specific value which is often given
xQT – 80% passing in undersize (microns)
xGT – 80% passing in feed (microns)
1.10 is a factor change (converts from short to metric tons)
Specific Grinding Energy:
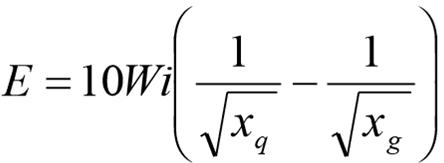
X.q – 80% passing in product (mm)
X.g – 80% passing in feed (mm)
Wi – Bond Work Index (kWh/t)
E – specific grinding energy (kWh/t)
The Abrasive Index
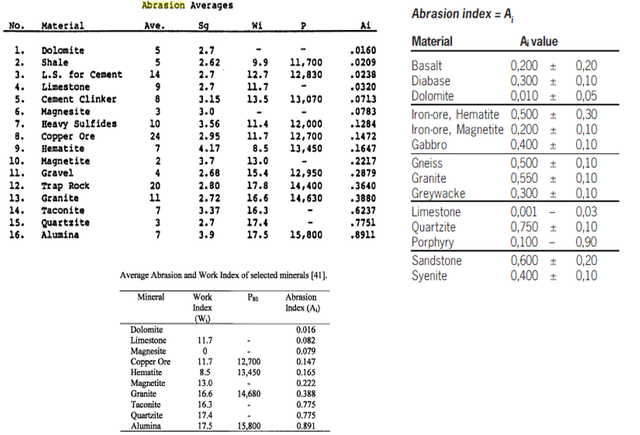
Table of Abrasive Index
This table is used identify which form of processing would be most optimal for that speific material as the Abrasive Index is used to identify its toughness in the form of abrasion (a physical property of the material).
After these calculations are completed and evaluated we may move onto the next step of the Communition process. Depending on the results from the above parameters, we will know which type of process to follow, that is, crushing or grinding.
Crushing:
In this process, the use of a crusher, which is a piece of equipment designed to produce smaller rocks from larger rocks, is used. A variety of crushers will be used as we will need to reduce the large mixture of minerals to smaller particles in a step wise manner. The following types of Crushers will be used:
- Primary crushing (of boulders)
- Secondary crushing (of materials from 100 mm to 10 mm)
- Ball or Rod milling (crushing of material from 10 mm to microns)
Each step in the crushing process must be done with precision as well as attention as the output of each step will become the input of the following step. The last stage, which is the milling stage, we will produce our final output of mineral. The principle on which the Crushers work are based on Intergranular Breaking Mechanisms and these breakages occur due to different forces such as compressive, impact and even shear, as well as abrasive.
For maximum optimization of crushing, the correct selection of the use of a crusher is extremely important. It will be dependent on the results of the calculations in the Size reduction step as well as the operating conditions on the day, the feed size of the solid mass, the capacity of the crushers as well as other properties such as the materials hardness and the degree of moisture of the feed mass.
Primary Crushers include:
Secondary Crushers included:
Elaboration of Crushers
Gyratory Crusher:
Before we learn the mechanism of a gyratory crusher, we should learn the different parts of the equipment and what they do. In the center of the machine, is a piece of equipment that we refer to as a Mantle. This is a moveable piece that will move from side to side causing compressive forces upon the large rock pieces that are dropped between the mantle and the concave. The concave, as illustrated in the diagram, is the fixed part of the equipment and acts as the breaking surface of the large rock pieces. Now that the 2 main pieces of equipment have being identified, we can move onto the mechanism of this crusher.
It must be noted first, that this diagram is a cross sectional area diagram of a Gyratory Crusher and in actuality, the crusher is a frustum shaped cone. When rocks are placed into the large top opening between the mantle and the concave, on both sides, the mantle will begin the move around in a circular motion to start applying compressive forces to all rock pieces in its capacity. Using this diagram, we will use the cross section to understand. When the large rock is added in the crusher at position 1, compressive forces will act upon the rock. When the mantle moves to it open position (refer to the above figure) the rock of smaller size (due to the rock losing mass due to the forces acting upon it) will move down to position 2. When compressive forces by the mantle act upon the rock once more, the rocks size will further decrease. From position 2 till 8, which is regarded as the choke zone, the process will repeat itself.
As the Mantle oscillates between the open and closed positions, the deforming rock will fall from position 1 to 8. As we move down the crusher, and while the compressive forces will act upon the rock, the distance of the closed positioned mantle and the concave will decrease. At position 8, the distance between these two positions will be almost 0 or very minimal. This point is referred to as the Choke zone
3D image of a Gyratory Crusher
The broken pieces of rock that break off due to the compressive forces will fall out through the lower exit. The broken pieces will also be inspected to identify if any materials of value will be contained within them. The larger circular rocks that “roll out” after position 9 will also be inspected as it is now easier to be inspected by hand by workers for removal of all valuable products. This branch of primary crushers has a large capacity and is suitable for feeds that are slabby as the principle forces of the Mantle’s crushing head are that of slow compressive forces.
Jaw Crusher:
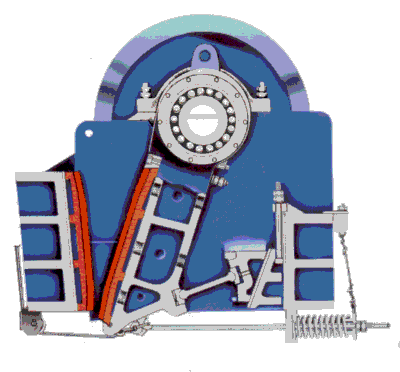
A Jaw Crusher
This is a form of a primary crusher that works in the following way:
Working on the principle of compression, large rock particles are placed at the wide entrance between the 2 orange plates (the colors are used for descriptive purposes only, they do not necessarily only come in that orange color). The V-shape that is made by the plates are composed of 2 parts, a fixed plate which is considered to be the surface that the rocks will break upon whereas the movable plate, which is pivoted at one end, is considered to be the plate that exerts a force upon the rocks by compressing it up against the stagnant plate. The distance that the moveable plates oscillates to can be varied.
This variation of space will allow us to make sure that only the desired size of crushed rock will be able to leave the Jaw Crusher. When a rock of a large size is dropped into the crusher through the larger opening, the crusher will begin to apply forces upon the rock causing it to break down. Once the rock has reached the desired size, it will be able to fall through the small opening at the bottom. If the rock has not being broken down to the desired size, it will stay in between the 2 plates until it is. The distance of the plates from each other is a major advantage to this form of Crushing, because it allows us to vary the spaces so a large range of rock sizes can be obtained.This form of crusher has a smaller capacity than that of a Gyratory Crusher but it is suitable for hard and abrasive rocks and is very easy to be operated. It is also exceptionally suitable for the crushing of ferro-alloys, as ferro-alloys portray extremely unfavorable properties such as an extremely hard and abrasive physical exterior.
Impact Crusher:
An Impact Crusher is the simplest form of primary crusher that works on the principle of compressive forces formed upon impact between 2 surfaces (hence the name). There are 2 branches of impact crushers, that are, Dynamic and Gravity Crushers. Dynamic Crushers are the more advanced type of crusher between the 2 branches.
A Dynamic Crusher could be described as a process whereby large rocks are broken down into small pieces by the use of a fast-moving circular rotor. Connected to this rotor are extremely tough materials and these materials are forced onto the rocks due to the rotational motion. Due to this motion, centrifugal forces occur and are forced upon the rocks during impact along with compressive forces. In addition, these pieces (once contacted with the rotor) will we be thrown against a tough surface to further assist in the breaking of the larger pieces. This will therefore cause the rock to crack and form smaller constitutes of the original big rock. An example of a Dynamic Crusher is a Vertical Shaft Impactor (VSI). It is given its name due to the fact that the shaft feed and output occur in a vertical line, that is, feed is added through the top and the output is extracted through the bottom, in the same line.
The Gravity Crusher results in the breaking of rocks through the impact caused due to the falling of rocks from a certain height above the breaking surface. The rocks are usually dropped onto plates that are made of highly abrasive material such as steel.
This brings us to the end of part 1 of Comminution, on my next post we will explore the other branches of Crushing as well as the Grinding step.
Images are linked to their sources in their description
The End
References:
[1]https://www.911metallurgist.com/blog/impact-crusher-working-principle
[2]http://www.mine-engineer.com/mining/jaw_crusher.htm
[3]https://www.911metallurgist.com/blog/choke-feeding-a-jaw-crusher
[4]technology.infomine.com/reviews/Crushers/welcome.asp
[5]https://www.911metallurgist.com/blog/bond-work-index-formula-equation
[6]https://www.911metallurgist.com/blog/table-of-bond-abrasion-index-for-varied-minerals-materials
[7] WILLS, B. A., & NAPIER-MUNN, T. - Wills' mineral processing technology: an introduction to the practical aspects of ore treatment and mineral recovery. Amsterdam(2006)
Being A SteemStem Member
Downvoting a post can decrease pending rewards and make it less visible. Common reasons:
Submit
Congratulations @akeelsingh! You have completed some achievement on Steemit and have been rewarded with new badge(s) :
Click on any badge to view your own Board of Honor on SteemitBoard.
For more information about SteemitBoard, click here
If you no longer want to receive notifications, reply to this comment with the word
STOP
Downvoting a post can decrease pending rewards and make it less visible. Common reasons:
Submit