Comminution- The art of Reduction (Part 2)
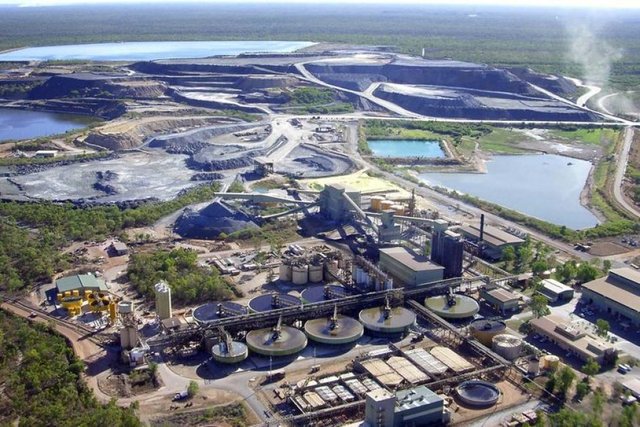
An aerial view of a mining site
On my previous post, I spoke about the aspects of Size reduction in the mining industry as well as an introduction into the topic of Crushing. As can be noted, from the previous post, a lot of preliminary processes and man hours have to go into the production of our jewels and gems. On this post, we will be further exploring the other branch of Crushers, that are, Secondary Crushers as well as the different types of Mills, that fall under the Grinding Process.
Elaboration of Crushers (continued)
A Cone Crusher is a form of secondary crusher that works almost similarly to a Gyratory Crusher but has no choke zone.
This crusher consists of a rotating mantle and attached to this mantle is a frustum shaped cone made of extremely hard, abrasive material. When large rocks are added into this crusher, from the top opening, these large rocks will sieve its way through so that it can be lodged between the rotating frustum and a hard wall surface to assist in the breaking of the rocks. When the rock is broken, these pieces of appropriate sizes will fall through once at the desired size.
There is, however, a flaw that was noted in the Cone Crushers design. If we draw our attention to the animation alongside, we will note that through the oscillation of the mantles’ attached frustum, the space between the mantles surface and the hard surface is constantly changing through the rotational motion. This seized as a problem because larger rock pieces were therefore making its way through these spaces without being crushed at all thus workers would need to manually remove these pieces by hand and refeed them into the crusher. To resolve this issue, the initial idea was to only let the rocks through a certain portion of the crusher, that is, by manipulating the mantle such that the mantle would not create such a large opening. To do this however, a certain portion of space between the mantle and the abrasive surface would have to be closed off. This would therefore add time to the production process as well as the additional costs in electricity to run the crusher. This form of crushing is referred to as the Closed Side Setting. The next, and more feasible, idea that they came up with was to create to second method of selection. Once the product of the crusher is sieved through, which includes the crushed pieces as well as the uncrushed pieces, the amalgamated lot would be sieved again and this time only the desired, crushed rocks will fall through while the uncrushed will not. These uncrushed pieces will then be recycled back into the original feed and will be re-crushed. Both type of crushers are still used today but the latter branch which incorporates the recycle stream is more popular due to its practicality and being more economical that the initial solution.
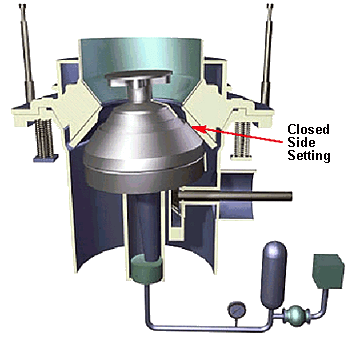
Initial Solution
Cone Crushers are excellent secondary crushers due its large capacity as well as its ability to crush strong and tougher rock minerals than that of primary crushers. Due to this reason, Cone Crushers are used extensively in the gold mining industry.
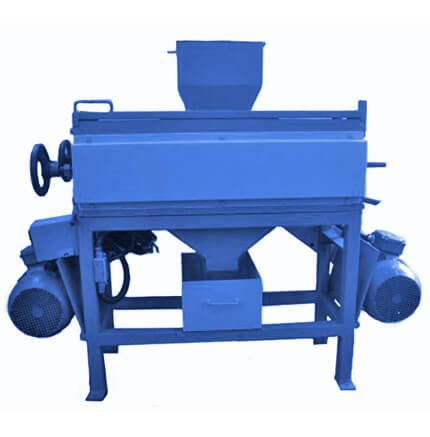
A Roller Crusher
A Roller Crusher is a much simpler secondary crusher than that of the aforementioned Cone Crusher, but where this crusher advances in simplicity, it lacks in capacity.
A Roller Crusher works on the principle of have large pieces of rocks fall between 2 rollers that spin in opposite directions. When the rock is contacted by any of these rollers (which is made of tough, hard material such as solid steel or reinforced super concrete), it will be pulled down into the space between these 2 rollers. Compressive parallel forces from both rollers will act upon the rock from both sides and will thus cause the rocks to shatter and break into smaller particles of the original big rock.
Due to the toughness of the rollers, a continuous feed can be supplied into the crusher as there will be an unlikely chance for jamming to occur. If it does occur, the crusher can automatically switch off and be fixed and must be manually restarted to prevent injuries.
Grinding:
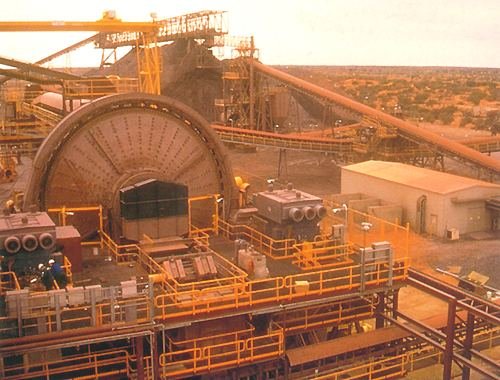
Grinding Equipment on a mining site
Grinding is a process which, just as crushing, aims for the same result which is further size reduction. If we recall from my previous post, crushing can only reduce the large rock pieces down to a minimum of 10 mm. Grinding can force these pieces of output from the crushing step to be even smaller, in a range of between microns up to 5 mm, therefore we regard grinding as a further reduction step.
The process of grinding is usually that of a powdering/pulverizing by the use certain forces such as impact forces, compression and shearing forces as well as attrition forces.
The main purposes of grinding can be split into 2 points:
- Liberation of useful minerals as well as gems that are trapped within the large mixture of rock
- To then use the mineral fractions to create fillers
To achieve these objectives of grinding, there are 3 methods
Amongst these 3 mentioned methods, in industry the most widely used is that of Tumbling, due to its simplicity as well as practicality. For that reason, we will be exploring a few of the most common Tumbling Mills.
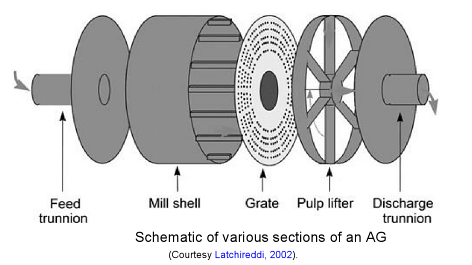
Parts of an AG Mill
AG mills are large capacity mills that take in feeds from a primary or secondary crusher or even the uncrushed ore as a whole. When initiated, the mill will start rotating. Since the shape of the mill is similar to a cylinder on its side, when the mill begins to rotate, the mixture of large and small ore pieces will stick to the rotating walls and begins to rotate as well. While rotating, gravity will act upon the ore pieces and will cause them to fall on the pieces of ore beneath them. This will cause the both pieces of ores to break and this process is repeated by all ore pieces. The mill is then opened and inspected to identify if the desired size is obtained. If not, the process is started again to grind the larger pieces into smaller pieces once more. An AG Mill is therefore referred to as a Self-Grinding Mill, because it does not use any additional equipment within the mill to assist with size reduction. AG Mills can be operated regardless of the amount of moisture present; thus it can grind both dry and wet feeds. Due to its large capacity, the ore feeds can be as large as 400 mm, which is too big for any crusher.
Semi- Autogeneous Mills (SAG):
A SAG Mill works on the principle to that of an AG Mill but the only difference is that a SAG Mill contains steel balls within the mill to assist in the grinding of the large ore pieces. These steel balls constitute between 4-12 % of the mills capacity when filled with the acceptable level of ore. Due to this addition, the SAG Mill is said to have a larger capacity than that of a AG Mill and it can also grind both dry and wet feeds (wet feed indicating that the feed contained 20 % water by mass). SAG Mills are famous for being large in size while other mills are rather much smaller. SAG Mills are usually found and operated on mining sites of gold and platinum while are also known to have applications in other industries such as nickel and silver mining too.
A ball mill is a scaled down model of a SAG Mill but it contains more steel balls than that of a SAG Mill. It contains roughly 30 % of its full capacity. Ball mills are known to be usually very small as they assist in the production of Portland cement and are used in the laboratory to make grinding samples to assess a materials’ grinding quality.
Rod Mills and Pebble Mills are similar to that of a ball mill due to its size but the only deviation is that these mills use steel rods of varying lengths in, and across, the mill and pebbles of varying sizes respectively.
Grinders are much better than crushers for size reduction because grinders can accommodate larger pieces of ores and rocks as well as moisture within these clumps of mass. It must be stated that crushers are extremely economical in the size reduction process. It is more feasible to use a crusher for smaller ore pieces and to use mills for larger ore pieces with the addition of the output from the crusher. This is because when the dry output of the crusher is mixed with the wet feed of the mill, during crushing, the dry crushed pieces will attach to the wet feed which will give it pseudo-shape and this will assist in grinding and overall size reduction.
Storage:
The storage of minerals after processing varies from site to site due to the capacity of the crushers and grinders as well as the plants site to accommodate them. Storage does however follow similar guidelines on all sites, although the only difference will be the sizes of these storage facilities, which once again depend on the plantations sizes. Storage is mainly needed for dry ore or pulp and storage is accomplished in either stock piles, bins or tanks.
Stock piles are used mainly for coarse or low valued ore and allows for blending of a variety of ores. The design of stock pile storage incorporates the factors of broken ore and weight and also is known to have conveyor systems for transportation of ore to the plantation from the stock pile.
Storage bins contain crushed ore and must be designed for easy transportation to the plantation site. Coarse material that ae offloaded from conveyer belts, railways as well as trucks are loaded into these bins for further movement on a plantation site. These bins are usually made of wood, steel or concrete and must be easy to fill as well as to empty through its discharge gate.
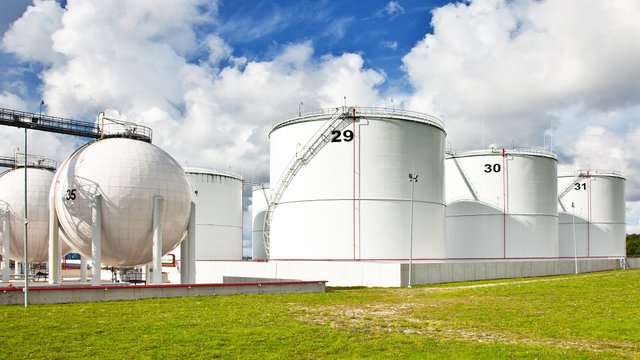
Storage Tanks
Storage tanks are used for pulp storage and these tanks require continuous agitation to result in good mixing of fluids and thus to avoid settling from occurring. These tanks are also often used during processing as it assists in smoothing out the differences of the input pulps feed rate.
This brings us to the end of another short series on an important aspect of mining. I hope that from this post, you have gained insight into the processes that occur daily to provide us with such beautiful objects.
Images are linked to their sources in their description
The End
References:
[1]https://www.911metallurgist.com/blog/cone-crushers
[2]https://www.911metallurgist.com/blog/roll-crushers
[3]http://www.ninekings.co.za/Cpx/30773/mining-ore-storage-bin.html
[4]https://en.wikipedia.org/wiki/Mill_(grinding)#Autogenous_mill
[5]WILLS, B. A., & NAPIER-MUNN, T. - Wills' mineral processing technology: an introduction to the practical aspects of ore treatment and mineral recovery. Amsterdam(2006)
Being A SteemStem Member
Downvoting a post can decrease pending rewards and make it less visible. Common reasons:
Submit