Cooling Methods
Refrigeration, commonly known as a cooling process, is more correctly defined as the removal of heat from a substance to carry it or keep it at a conveniently low temperature, below the ambient temperature. The most widely used method for producing mechanical refrigeration is known as the vapor compression refrigeration system. In this system, a volatile liquid refrigerant evaporates in an evaporator; this process results in a heat removal (cooling) of the substance to be cooled.
Figure 1 shows the arrangement of the equipment and the interconnection pipe of the basic steam compression system. The four basic components of the system are the expansion device (also called flow control device), evaporator, compressor, and condenser.
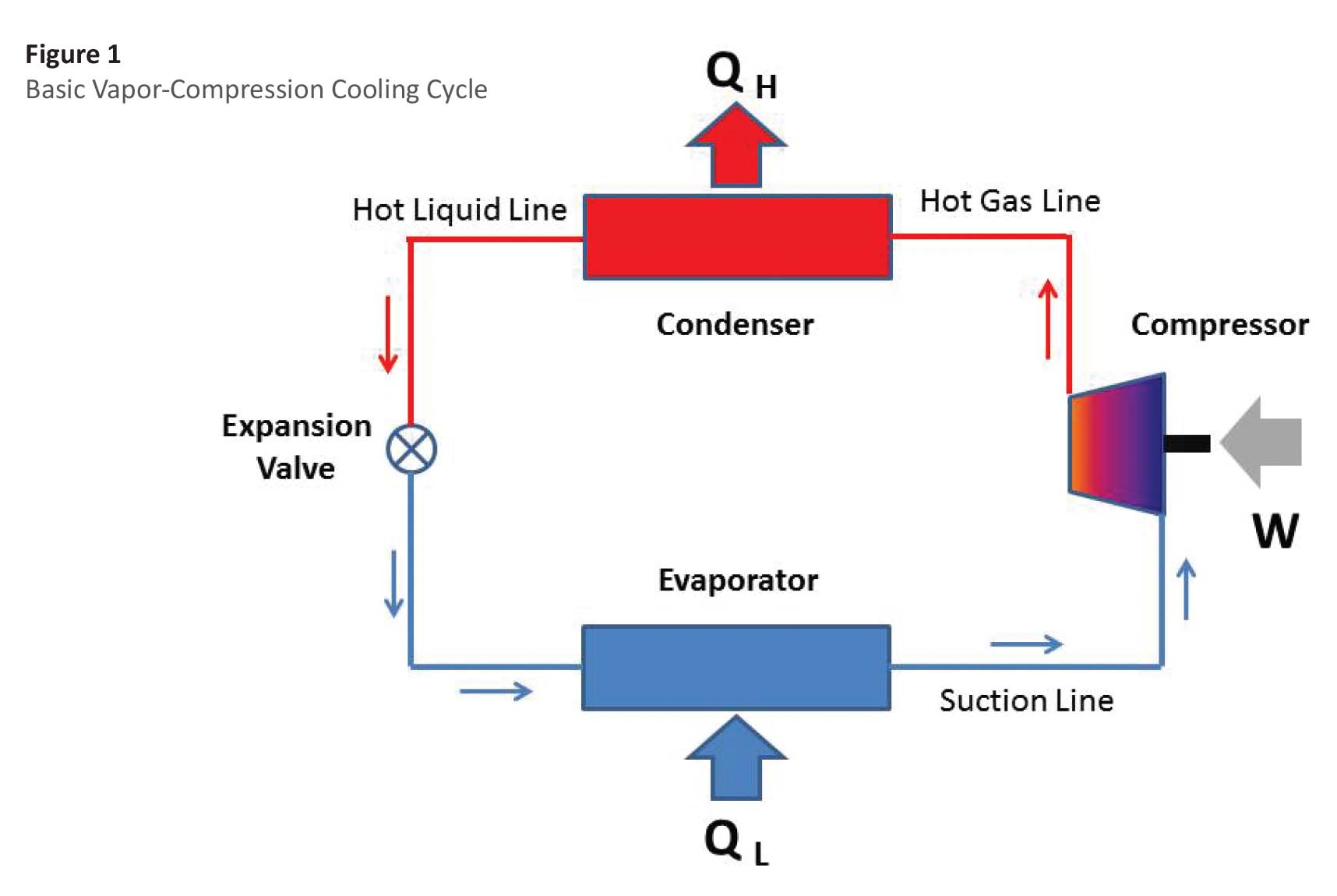
Flow control devices (expansion) of the refrigerant
The flow control device must perform two functions in a vapor compression refrigeration system.
It must regulate the flow of liquid refrigerant that is fed to the evaporator, according to the demand.
You must create a pressure drop, from the high side to the low side of the system. This pressure drop results in the expansion of the flowing refrigerant, causing a small amount of it to evaporate so that it cools down to the evaporation temperature.
In most cases, the flow control device must feed the liquid refrigerant to the evaporator in the same proportion as the compressor pumps it from the evaporator. That is, the evaporator must not be overfed or underfed. The flow control device must react to a change in conditions, which in turn require a change in the flow. When the thermal load in the evaporator increases, the flow control device must react and feed more refrigerant and must reduce the flow when the load decreases. In the market, there are different types of flow control devices, which perform their function differently, and some of them do not do so satisfactorily under certain conditions, that is why each one has different applications.
All flow control devices have a restricted opening or passage, which creates the pressure difference necessary to carry out their expansion functions. Most devices are built like valves; that is, the restricted passage can be opened or closed, and in some cases, it can be regulated between fully open and totally closed. These types include the manual expansion valve, thermostatic expansion valve, high and low side float valves and automatic expansion valve.
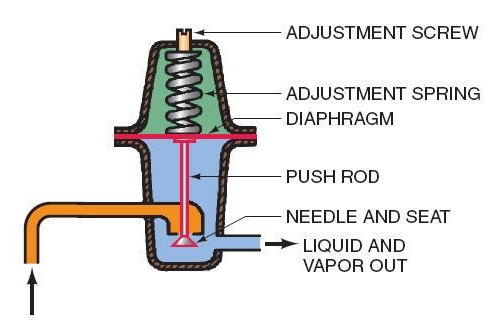
Evaporators
The evaporator constitutes (together with the condenser) an example of the type of equipment known as a heat exchanger. It aims to provide a continuous and efficient transfer of heat from the medium to be cooled to the refrigerant fluid. The medium to be cooled can be a gas, a liquid or a solid. In the most common evaporators, the refrigerant flows through the tubes, while the fluid that is to be cooled circulates on the outside thereof.
The refrigerant enters the evaporator pipe at low temperature and low pressure, as a result of the expansion it experiences when passing through the flow control device (figure 1). A small portion of the refrigerant evaporates due to the sudden drop in pressure, cooling the remaining liquid, as well as the vaporization gas itself. The temperature of the refrigerant is controlled to a desired value, below that to which it is desired to cool the other fluid, by selecting the appropriate equipment and using control devices. One way to classify the evaporators is according to the relative amount of refrigerant in the form of liquid and vapor flowing through the evaporator. In the dry expansion evaporator type, the amount of refrigerant fed by the flow control device is just enough to evaporate in its entirety before leaving the evaporator
Although there are probably hundreds of different shapes and arrangements of the heat transfer surface of the evaporator, they can almost always be classified into two types: tubular or plate. Tubular heat transfer surfaces can be subclassified into plain tube types and finned tubes. The fins are used in the pipes or pipes in order to increase the surface area, thus increasing the heat transfer per unit length of pipe.
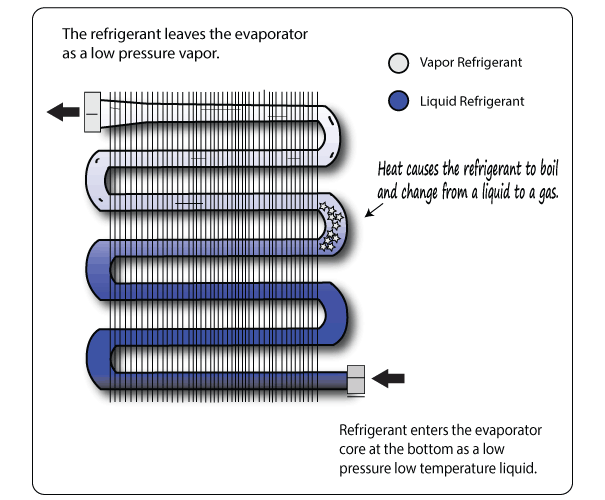
Compressors
The main function of a refrigeration compressor is to increase the vaporization pressure, up to the pressure at which the gas can be condensed. The pressure must be increased until the saturation pressure corresponding to the condensation temperature is reached. The high discharge pressure provides the necessary energy to make the refrigerant circulate through the pipe and the equipment. In addition, the large pressure differential created causes the sudden expansion of the flow control device, causing a temperature drop. Refrigeration compressors can be classified into two main groups, depending on how the gas pressure increase is achieved. Those of the first group are called positive displacement and those of the second are called dynamic compressors. There are three types of positive displacement compressors: reciprocating, rotary and helical. There is only one type of dynamic compressor that is used in refrigeration processes, called a centrifugal compressor.
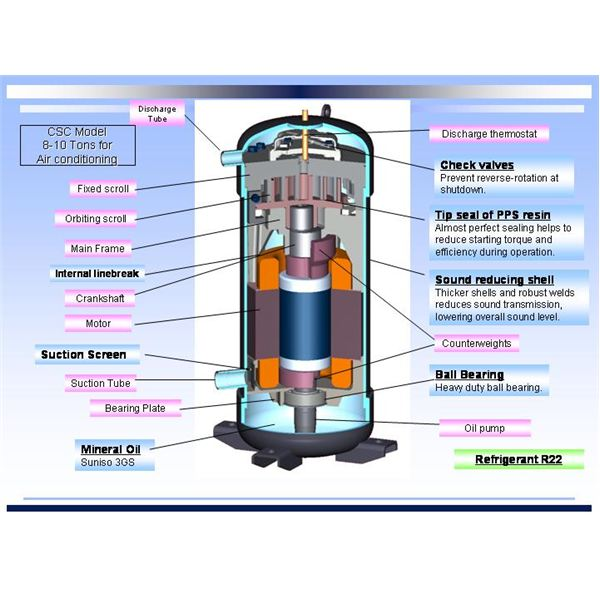
Condenser.
In the condenser the operation is just contracted to that of the evaporator, in the case that the refrigerant vapor, being compressed in the compressor and entering the condenser in the form of vapor (refrigerant gas) at a high pressure and also high temperature, allows the exchange of temperatures with air, water or any fluid; this achieves that all the heat of the refrigerant that was absorbed from the evaporator is given away, which will now be discarded to the environment (or any other fluid). The condenser must pass the vapor refrigerant to saturated liquid (subcooled liquid), so that it always remains liquid on its way to the evaporator. Are the teams in charge of transferring out of the refrigeration cycle the heat absorbed in the evaporator and in the compression stage. They do this by condensing the refrigerant vapor from the compressor. The function of the condenser is to transform the refrigerant gas compressed in the compressor into a cooling liquid. Inside the condenser, the refrigerant gas loses the heat absorbed during the process of its evaporation from the space to be cooled, as well as delivering the heat absorbed during its circulation through the return line to the compressor and the heat absorbed during the compression phenomenon inside the compressor.
Due to this delivery or loss of heat and the high pressure to which it is subjected, the gas is condensed and constitutes a source of coolant in the liquid state under conditions of being repeatedly delivered inside a refrigeration unit, producing consequently the cooling effect sought.
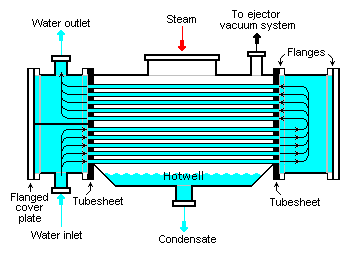