No matter what type of business you own, it is imperative to keep everything running smoothly at all times. That is why you should keep your electrical equipment well maintained.
Read this article to find out more about different maintenance types and various care strategies to decide what kind of maintenance your electrical equipment needs.
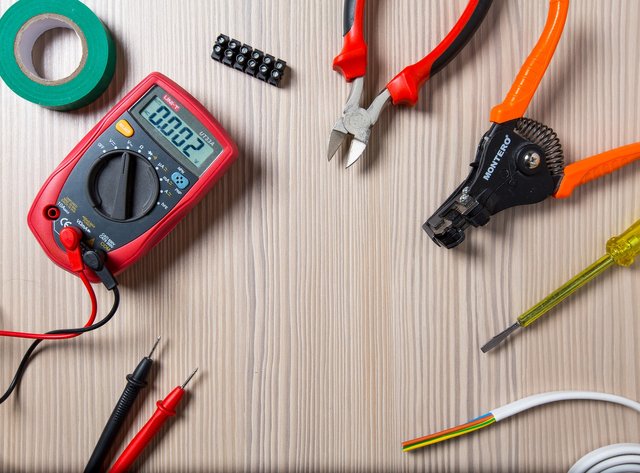
The basics
Electrical maintenance is the upkeep and preservation of equipment and systems that supply electricity to a residential, industrial, or commercial building.
The main areas of general electrical maintenance commonly include the power outlets and surge protectors, generators, and lighting systems. These supply sources are checked for structural integrity as well as internal stability.
When it comes to electrical maintenance types, the jury is still out on the kinds of care you should provide your electronics. But, most experts agree that there are four types of it that your electronic equipment needs on a regular basis.
Reactive maintenance
This approach is also known as breakdown or run-to-failure. Reactive maintenance has a pretty simple strategy: fix things when they break.
This is an excellent method to employ for equipment that is not essential for operations or has a low cost since repairs are not planned. Because of this, this concept is only worthwhile if you are dealing with things that are rarely used or duplicate the function of other equipment.
One clear advantage of this approach is that it requires minimal planning on your part. It is clear why this should not be your only strategy, as it has several drawbacks that outweigh its qualities.
If the approach is used for all equipment, there can be considerable production delays when a critical piece of equipment fails. Additionally, if you do not have the right parts and supplies on hand, rushed shipping costs can become significant.
Overall, reactive maintenance often means more downtime and higher maintenance costs when it is not used strategically. You should use it only when there is no alternative.
Preventive Maintenance
On the opposite side of the spectrum, compared to reactive maintenance, we have the preventive one. It is aimed at catching and fixing problems before they happen. It is most commonly carried out in regular inspections, usually occurring multiple times per year.
Preventive maintenance involves carefully checking for all signs of wear, tear, or imminent breakdown. If you notice that something is not up to standards, replace damaged parts immediately. This will prevent a crisis that could happen if something breaks down unexpectedly.
This type of maintenance is also referred to as planned since it is based on well-established maintenance programs and hard facts. Its purpose is to extend the useful life of an asset and prevent breakdowns from occurring.
At a glance, this approach might seem like the one that is always ideal to use, but that is not the case. If the surveillance schedule is not regularly monitored, audited, and improved, technicians could get bogged down by unnecessary tasks and cost the organization time and money.
Besides, too many checkups can lead to post-maintenance breakdowns. This can happen because of defective replacement parts, a maintenance regime that is too robust to function appropriately, overlooked damage occurring during an inspection, and many other reasons.
Condition-based maintenance
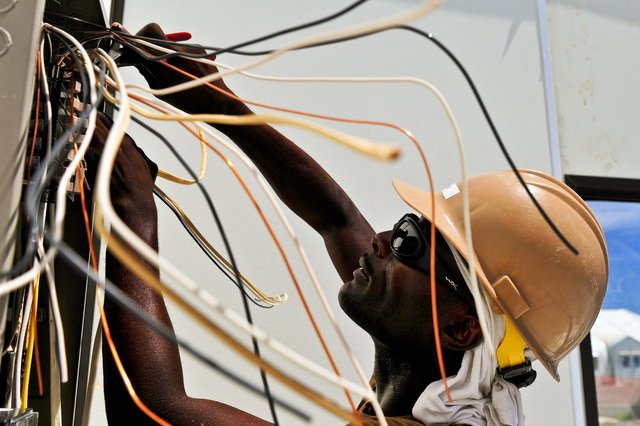
Somewhere in the middle between the two maintenance strategies mentioned above, we have condition-based maintenance.
This is when, instead of being inspected according to a schedule, machines and systems are carefully observed for changes that could indicate impending failure.
During this process, you should observe the system running and identify variables that could affect functioning, like temperature, vibration speed, power, the presence or absence of moisture, and more. Another name for this approach is predictive maintenance.
The advantage of predictive maintenance is its potential for cost savings from reduced working hours spent on care and more insight into the performance and potential issues arising with the machine.
Also, it involves reliance on data and sensor information. This means that maintenance is determined by the actual condition of equipment, rather than a best-guess schedule or a simple visual inspection.
The predictive approach is the most intensive type of maintenance. This is because there is a lot of data to interpret – and the sensor devices themselves need to be regularly maintained and checked. It is also very time consuming, at least initially. You would have to first build on the processes and insights that preventive maintenance provides to create an effective predictive maintenance plan.
Reliability-centred maintenance
Out of all the different strategies listed here, reliability-centred maintenance is the most involved one. It seeks to analyze all the possible failure modes for each piece of equipment and customize a maintenance plan for each machine, with the ultimate aim to increase equipment availability and reliability.
Unlike other styles, this type of maintenance is carried out using rules and suggestions created by the original manufacturer rather than the maintenance team.
The most significant advantage of this plan is simultaneously its biggest downside. Because each piece of equipment is analyzed on its own, the result of going through with a reliability-centred maintenance effort may be having as many different maintenance plans as you do pieces of equipment.
This could be too demanding, so maybe equipment with a higher risk and a very high chance of failure should be subject to more frequent maintenance and inspection. Low-risk equipment can be maintained at a much lower frequency and possibly with much smaller work scope.
Conclusion
When it comes to electrical equipment maintenance, there is no universal solution to cover all of our risks. The best approach would be a healthy mix of the strategies listed here; all of them are organized in a tight schedule to minimize the risk of failure.
Keep in mind that every approach mentioned here has its advantages, but it comes with its downsides as well. In the end, you are going to have to be the final judge and determine which approach offers the best risk-reward ratio for you and what works and what does not for your business.